
Not far south of Dromahair at Creevelea and Arigna are found the traces of three significant industrial developments based on the natural resources in the region, those of coal, their underlying fireclays as well as the significant reserves of iron ore . The industrial history continued with mining, the Arigna power station until the 1980s, experimental biomass, to the present day with Arigna Fuels on a historic site and most recently, wind power generation.
Previous to the mining of coal when the intensive felling of woodlands of oak, ash, birch became depleted, their charcoal being used to fire the iron furnaces according to credible legends, possibly far beyond existing written accounts (which date iron working activity to the 1400’s).
Leitrim Clays
The abundant Leitrim clay or daub useful for red earthenware was also used to make low temperature common brick nearby in Friarstown and reportedly at the ‘Factory Cross’ near Belhavel.
Pottery
There is no evidence of glazed pottery in Leitrim before the plantations. With the ending of the O Rourke chieftains’ rule, English planters brought with them a number of tradesmen, including potters. Brian Mc Cuarta writes in p.317 of The Plantation of Leitrim 1629-41 the following :
For example, pottery was made in Leitrim village and at Keeldrin , Newtowngore, including lead and manganese black glazed crocks, located as in the 1837 maps below. A brick Claypit can also be seen in the map at Killarcan, Glenville just north of Leitrim village.
Leitrim Fireclay Production at Lugmore and Spencer Harbour
The coal base fireclays are of a different nature, capable of being fired to a very high temperatures (~1400oC) and were in the 19th century exploited at Lough Allen, where the 50 ft high chimney of a large brick kiln may still be seen.
“In the Lough Allen coal field, beds of fire-clay are found, of which that forming the seat of the Crow coal varies from a few inches to three feet in thickness at the edges. In the valley of the Arigna this bed was found uniformly three feet thick, and of excellent quality, the whole of the bricks used at the iron works, by the original proprietors, having been made of it; …..Under the three foot coal lies another and similar bed.” The Industrial Resources of Ireland (Author: Robert Kane) Ch.6
At Creevelea Ironworks, fireclay may have been also worked as ‘kilns’ are clearly marked on the early maps there on the level near the upper road, above the huge smelting tower
Spencer Harbour Clay Works 1871-1883
A schoolboy’s description in 1938 from the Dúchas collection :
Spencer Harbour
Some years ago a company started an industry, known as a pottery on the shores of Lough Allen, in which they made all sorts of chimney pipes, eave pipes, sewer pipes, bricks, and crockery.
A boat named Lady Spencer came there to take away some of the earthenware to Limerick and sometimes to England and Scotland. One day the boat became wrecked a few yards from the shore and was dashed to pieces.
The part bearing the name Lady Spencer floated into the harbour, and immediately a man called the place Spencer Harbour.*
By and by the industry was closed down, and till this day there can be seen a high chimney and a pier where the boat anchored. Nowadays the Leydon family lives there.
by John Guihen, Cartron, Loch Allen, heard from from:- Phillip Flynn, (78) , 28th February, 1938
*Note: Mr Flynn’s information to the schoolboy John Guihen was possibly more entertainment than fact as there is no record of the boat or the unfortunate events described. However Earl Spencer was Lord Lieutenant twice in the years of the company’s existence.
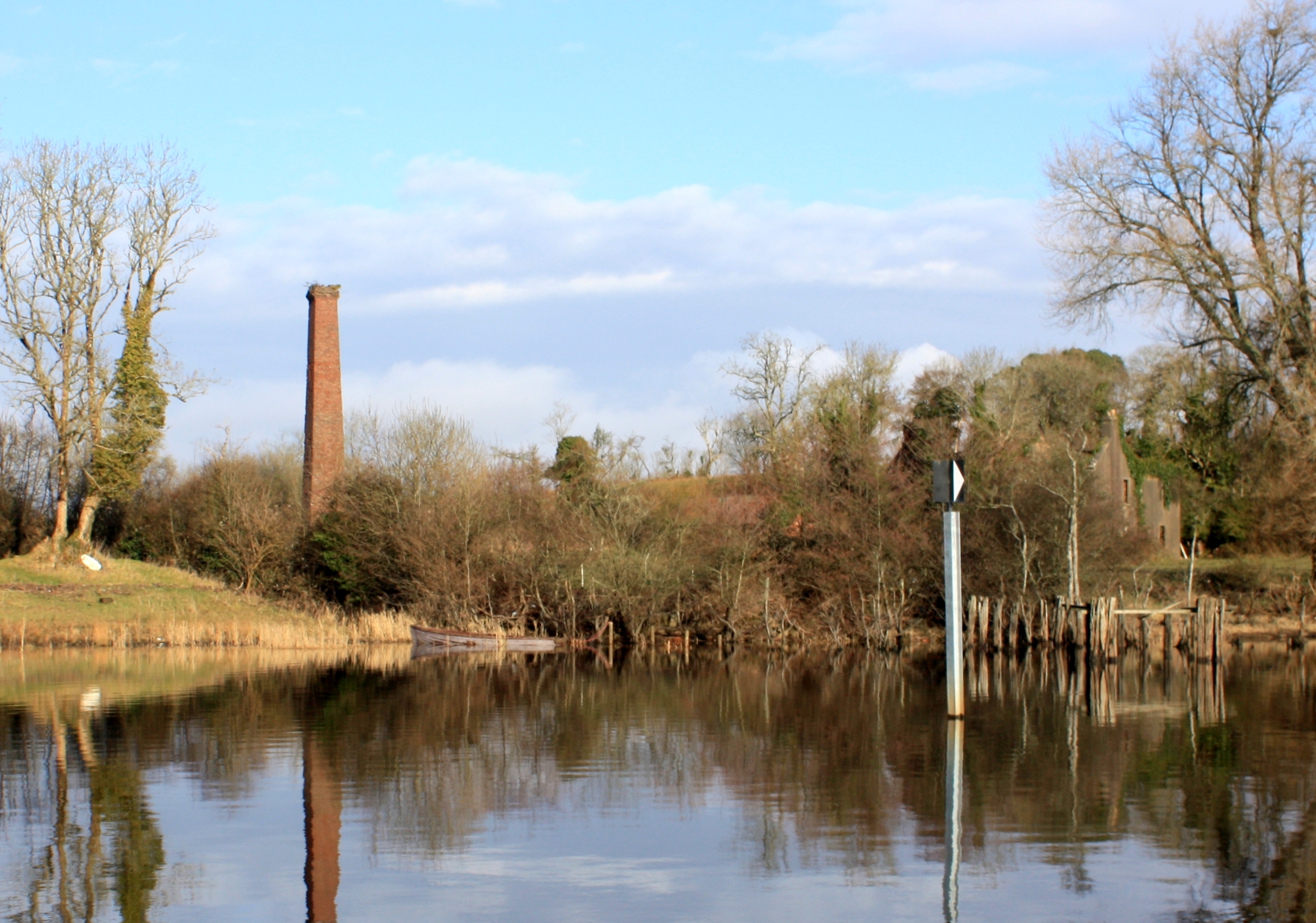
Chimney of brickworks and remains of jetty at Spencer Harbour
Related to mining and coal production in North Leitrim was the Lough Allen clay company, operating between 1871-1883 . This was not the first or the last local firebrick company, as another enterprising local venture at Lugmore preceded it, following the discovery of a new seam of coal on a bed of good fireclay, as is described here:
Excerpt from “A way of work and a way of life” by Breda & Sean Wynne
” On Mc Dermott’s trips to Lugmore on each consecutive Saturday for culm, he inspected the brick ovens, four in all. The outer one being built of stone, while the inner one was built of brick, the building comprised of four cells and about 3’6’ high with a countersunk cavity on top, on which metal plating had been fitted, a coal fire was lit in each individual cell and when the plotting was sufficiently hot the already shaped fireclay would be placed in brick form to be baked.”
Note: This kiln description is curious as they seem small for brick ovens and any raw clay needs to be very gradually heated to drive off moisture , unless it describes preheating the kiln and ware before an actual firing. Also any ‘metal plating’ would melt in the extreme heat above 1000 degrees needed for durable fireclay.
“The fireclay was in a plentiful supply in the hillside behind the ovens. The Jetty Brick Company was credited ( with the change ) from making all the bricks here by this outmoded method, (as) they built a modern brickworks on the shores of Lough Allen at Spencer Harbour .
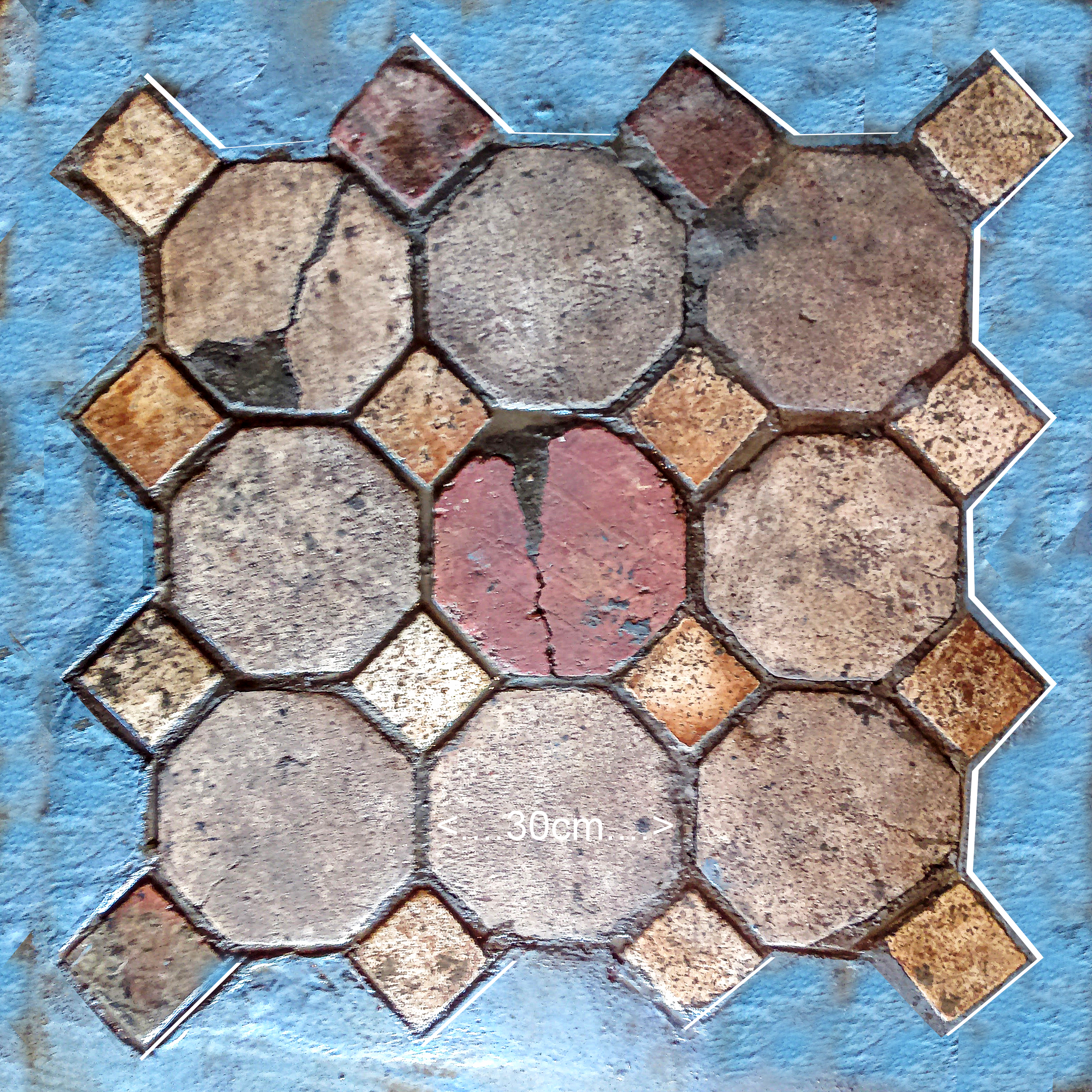
Large French style octagonal 30cm Floor Tiles, some salt or fire ash glazed, reclaimed in 1985 from Spencer Harbour old post office.
“The 50 ft chimney stack on the shores of Lough Allen still remains as a monument to the Company’s memory…. The Company was a British concern, as also were the workers. Milo Lyons supplied the necessary coal. Lough Allen brick stamped with the company crest is still to be found on the shore.”
“….the clay works had been “brought to such a success” that there was a backlog of orders and that additional capital and boats were necessary. There was “every description of clay” at Lough Allen including some fine white clay suitable for pottery, which, however, was not made. But virtually everything else was – fire bricks, sewerage and drainage pipes, bricks, tiles and moulded plaster-of-Paris goods. The manager was “a first-rate Staffordshire man” who dispatched boatloads of sewerage pipes for such places as Woodford, Killaloe, Galway and Roscommon, and “high-class fire bricks” to Dublin for such customers as the Alliance Gas Company, Guinness’ Brewery and Roe’s Distillery.
From 1877 to 1882 the collieries were worked by the “Lough Allen Clay Works Limited” the mine manager being James Lyons, who from 1883 worked the mines in his own right. Associated with the coal in this region were deposits of fire clay which gave very fine bricks and which appear to have been worked from Buchan’s time onwards, if not earlier, and it was this resource which resulted in the setting up of the clay works in the mid-1870’s. As will be noted there is a considerable degree of mystery about this concern, which burst on the scene about 1873 and just as dramatically disappeared less than a decade later. One rather improbable reason was advanced in 1923 by Major in evidence to the Canals and Inland Waterways Commission, Dublin, 23 January 1923 who also commented on the setting up of the works
“One of the late chief engineers of Guinness’ who left Guinness’ with £40,000, went up to Lough Allen and at the extreme end started a brick and tile works. He left it there and left all his money there because the [Lough Allen] canal, even in those days, was worse than in our day.”
Certainly, the canal was far from perfect but if the works were as good as the owner claimed in 1881 it is unlikely that they would have been abandoned six months later. Indeed, he stated that the works were only just finished and that there was “every prospect of an increasing trade.” Waller in evidence to the Monck Commission on Waterways, 1ST October 1881.
The managing director of the “Lough Allen Clay Company”, as it was also described, was George Arthur Waller, who also worked boats of his own between Lough Allen and Limerick. By 1881 three steamers and three barges were in use. It was necessary to hire barges at times; Waller also had to hire boats periodically to tow barges – in mid-1880 steamers of the Midland Great Western Railway were performing this task, though probably on the Royal Canal, along which Waller’s boats also went. Unfortunately, it was not possible to use the boats to anything like their full capacity because of the restrictions imposed by the Lough Allen Canal (size of the locks) – The width of the lock is 18” less then the locks on the Shannon.
Waller’s boats were specially built for the Shannon and had extra large boilers to enable them to burn the locally mined coal which was suited “admirably” for the clay works although it was “very brittle and dirty” and was not saleable except, to a small extent, in Athlone. However, when English coal was more expensive, considerable quantities were sent to Dublin, Limerick etc., and sold at thirty shillings a ton. Waller benefited from the heavy up-river traffic of the period and his returning boats were fully loaded. There was unsuccessful competition with the Grand Canal Company for the flour traffic from Messrs Russell of Limerick to Carrick-on-Shannon, but Waller prospered nonetheless and his boats drew a considerable amount of goods for Ballinamore – flour, Indian corn, petroleum, salt herrings etc. – although they were delivered at Drumshanbo as the Ballinamore & Ballyconnell Canal was by then virtually beyond redemption.
Oddly, in view of their impending sudden death, Waller maintained that the clay works had been “brought to such a success” that there was a backlog of orders and that additional capital and boats were necessary. There was “every description of clay” at Lough Allen including some fine white clay suitable for pottery, which, however, was not made. But virtually everything else was – fire bricks, sewerage and drainage pipes, bricks, tiles and moulded plaster-of-Paris goods. The manager was “a first-rate Staffordshire man” who dispatched boatloads of sewerage pipes for such places as Woodford, Killaloe, Galway and Roscommon, and “high-class fire bricks” to Dublin for such customers as the Alliance Gas Company, Guinness’ Brewery and Roe’s Distillery.
According to Waller some £15 a month was paid in tolls for his boats. The only available record is the toll account book for the Battlebridge lock on the Shannon Navigation, including the Lough Allen Canal. The figures given below cover the period 1871-1883 and they reflect the appearance, life span and sudden death of the clay works. Although some of the sums are tiny they are, in fact, the yearly total amounts collected by R. Hewitt at Battle Bridge Lock.
Year |
Amount |
Year |
Amount |
1871 |
£0-8-0 |
1878 |
£24-18-11 |
1872 |
£1-16-4 |
1879 |
£31-13-1 |
1874 |
£43-18-7 |
1881 |
£60-6-5 |
1875 |
£28-8-1 |
1882 |
£10-11-3 |
1876 |
£17-11-5 |
1883 |
£6-7-5 |
1877 |
£26-12-4 |
Thus both the colliery records and the canal tolls both show the last year of operation of the clay works. The latter are more specific – in the first three months of 1882 the tolls came to £8-9-6, for the next six months the total was a mere four shillings!
Arigna Ironstone 1903
There is a later mention at the Cork ‘International’ Exhibition of items of Clay Ironstone being manufactured in the immediate area :
Arigna Mining Co., Ballinamore, Co. Leitrim—Samples of Clay-Ironstone and articles manufactured there from Harrington Bros
Click to access 1903_catalogue.pdf
Links
Pingback: Spencer Harbour | Irish waterways history
Many thanks for the recommendation.. best wishes with your great site .
LikeLike
Delighted to come across your description of the brickmaking enterprise at Spencer Harbour on Lough Allen. I’m currently writing a history of brickmaking in Ireland and trying to record as many known locations as possible. I’d love to get in contact with anyone who would be willing to talk to me about the Lough Allen works, or indeed about any of he other brickmaking locations in Co. Leitrim. Susan Roundtree
LikeLiked by 1 person
Hi Susan, thanks for your reply and interest in our article . Will email you about information at hand about brickworks in and around Leitrim.
LikeLike